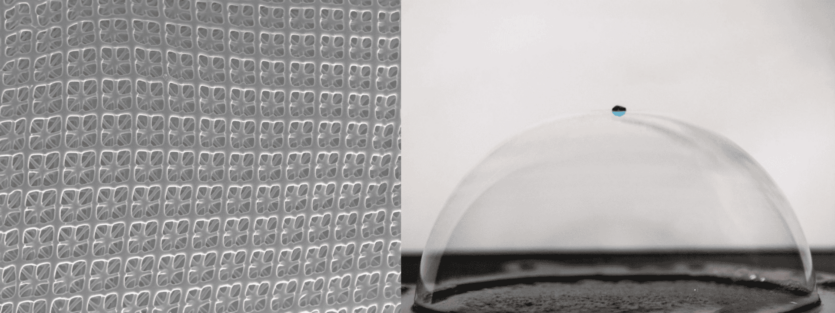
Researchers at the University of Toronto have developed a unique material by combining machine learning (ML) with nanotechnology. This discovery could dramatically change entire industries, from aerospace to automotive.
Engineers have been trying for decades to create materials that are both lightweight and extremely strong. This is especially important in the aerospace industry, where even a slight reduction in weight can significantly save fuel and improve efficiency. Traditional materials such as aluminum and titanium have their limitations, and carbon fiber, while revolutionary, is not the ideal solution.
Canadian scientists have decided to use nanostructured materials that mimic natural shapes, such as bones, shells, or honeycombs. They created geometries that distribute the load evenly, avoiding weak points where fracture could occur.
To find the optimal shapes, the researchers applied Bayesian optimization — a machine learning method that helps to choose the best option among many possible ones. They used data from thousands of computer simulations to determine the most efficient shapes for their carbon nanorods.
How does the technology work?
«Nano-architected materials combine highly efficient shapes similar to triangular structures in bridges, but at the nanoscale, allowing for a record strength-to-weight ratio», explains Peter Searles, lead author of the study.
The algorithm created thousands of possible structures that were tested in a virtual environment using the finite element method (strength calculations). The computer program then gradually refined these designs until it found the optimal structures with maximum strength and stiffness at minimum weight.
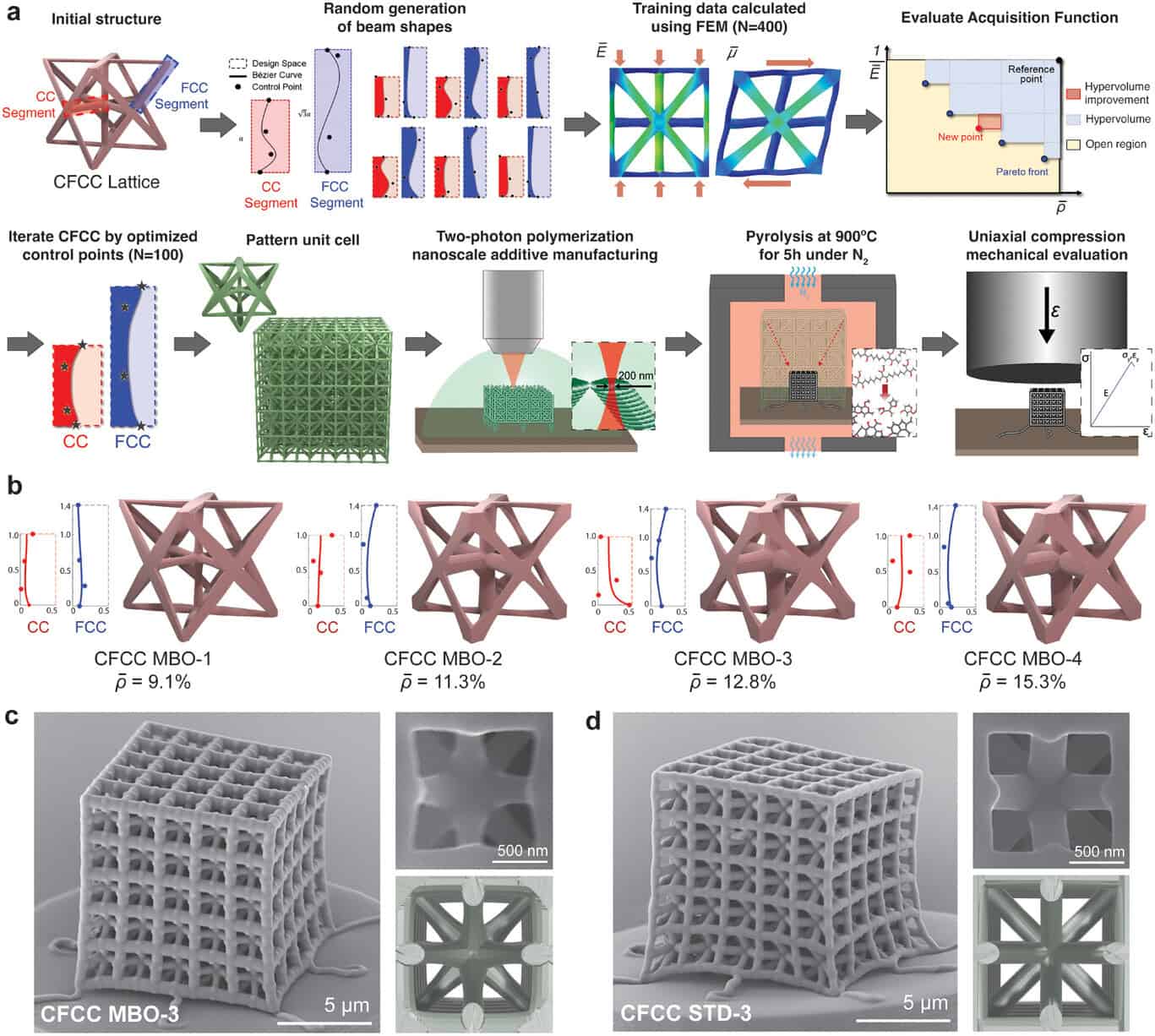
The researchers reproduced the selected designs physically using two-photon polymerization — a 3D printing method with nanometer precision.
They created gratings consisting of structures only 300 to 600 nm thick. These gratings (6.3×6.3×3.8 mm), consisting of 18.75 million individual cells, were then subjected to pyrolysis — heating to 900°C in a nitrogen environment, which converted the polymer to glassy carbon.
The optimized nanolattices more than doubled the strength of previous structures. They withstood a load of 2.03 megapascals per cubic meter per kilogram of density. To put this in perspective, this is more than 10 times the strength of many lightweight materials such as aluminum alloys or carbon fiber. They are also 5 times stronger than titanium.
«This is the first time that machine learning has been used to optimize nanostructured materials, and the results were impressive,» says Searls. «The AI didn’t just replicate known successful geometries, it created entirely new efficient shapes.»
Interestingly, the smaller the nanolattices, the stronger they are. This is due to the «size effect» — a phenomenon in which materials on extremely small scales behave differently.
The scientists found that when the diameter of carbon beams was reduced to 300 nanometers, their strength increased dramatically. This is because at the nanoscale, carbon atoms are lined up in structures that provide maximum rigidity. The outer layer of the beams consisted of 94% sp²-bonded carbon, which is known for its exceptional strength. Thanks to this, the material can withstand enormous loads without breaking.
Practical application
This breakthrough could significantly change the aerospace industry, the production of airplanes, helicopters and spacecraft. Lighter parts will reduce fuel consumption and reduce emissions.
«For example, replacing a titanium component of an airplane with our material can save 80 liters of fuel per year for every kilogram of material replaced,» Searls notes.
The researchers plan to scale up their developments for commercial use. Their next steps will be aimed at creating full-fledged structures with these materials while maintaining their strength and lightness. They also plan to continue searching for new designs that will further reduce the density of the material without losing strength.
Spelling error report
The following text will be sent to our editors: