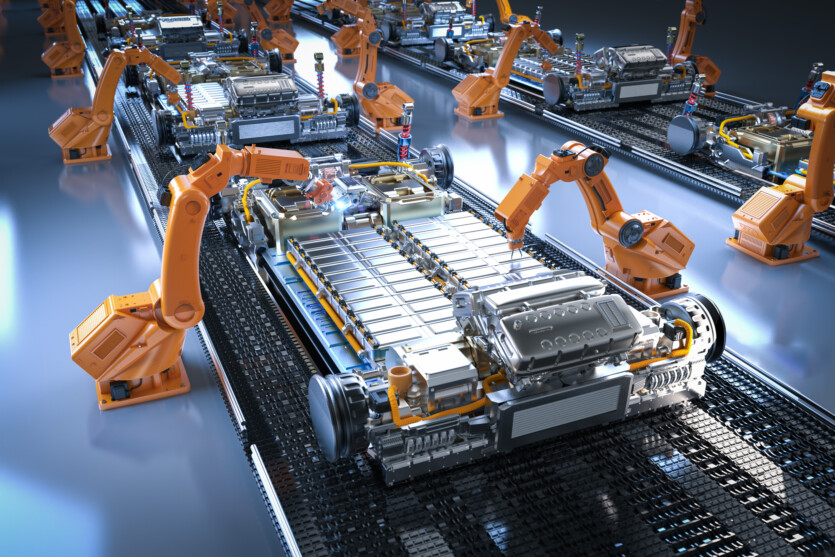
A group of South Korean researchers has developed a new printing technology that more than doubles the stability of lithium-metal batteries in electric cars.
«Providing ten times the theoretical capacity of conventional lithium-ion batteries, lithium metal anodes are a key material in solid-state and lithium-sulfur batteries that require high energy density. However, the risk of dendrite formation during charging/discharging cycles raises safety concerns, including the risk of short circuits and fire, and limits battery life», — the researchers explain.
The technology, proposed by researchers from of the Korea Research Institute of Chemical Technology (KRICT), allows to solve problem of occurrence needle structures — dendrites on the lithium surface. According to the results of battery pack tests, the lithium anodes protected by the new technology demonstrated 81.5% retention of the initial capacity after 100 charge-discharge cycles and a Coulombic efficiency of 99.1%.
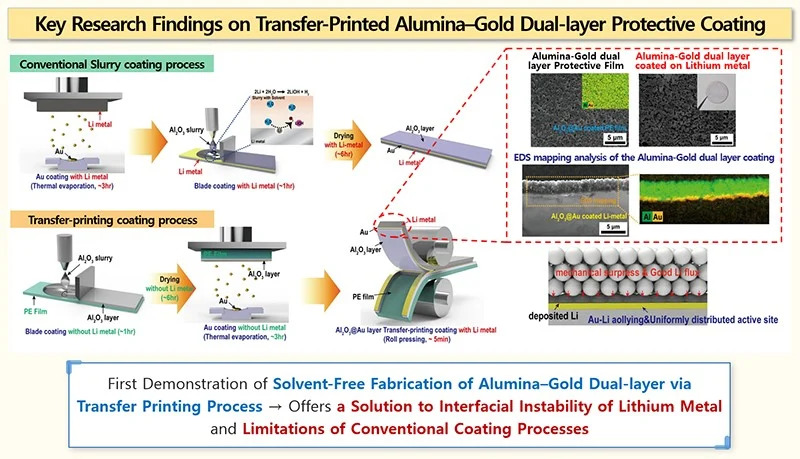
This is more than twice as much as stability of unprotected lithium cells. Even at high discharge currents, when the battery is completely discharged in 9 minutes, the cells retained 74.1% of their capacity, demonstrating stability in difficult conditions.
Researchers led by Dr. Chongdong Suk instead of the traditional «wet coating» processes based on the use of solvents, developed a solvent-free transfer printing method based on roll-to-roll technology. The reason is that solvents can damage highly reactive lithium.
«The research team has developed two types of protective layers: a double layer consisting of aluminum oxide (Al₂O₃) and gold (Au), and a hybrid layer combining ceramic (Al-LLZO) and polymer components», — the developers specify.
The process involves creating an ultra-thin, about 5 micrometers, hybrid protective film of ceramic and polymer on a separate sheet and then laminating it directly onto the lithium surface under pressure. This approach prevents damage and ensures uniform coverage.
«This study combines novel protective materials and a scalable transfer printing process to overcome critical interfacial instability and wet processing limitations in lithium metal batteries», — says Dr. Jeongdong Suk.
The team has already demonstrated the scalability of the method by successfully covering an area of 245×50 mm with a protective film. This development is expected to accelerate the practical use of high-energy batteries not only in electric vehicles but also in large-scale energy storage systems.
Source: Interesting Engineering
Spelling error report
The following text will be sent to our editors: